CBB – ADVANTAGES AND POTENTIAL OF A MINIMUM ENTERPRISE IN THE MARKET OF DRAWING PRODUCTION
According to Mr. Nguyen Khac Van, in the early days of establishing the CBB team, there were many difficulties in terms of human resources and resources. With the spirit of respecting intellectual property, finding the answer to the problem of allocating software copyright reasonably to the team and the somewhat limited financial capacity of a small company that has just come into operation. is a big challenge. Mr. Van and the CBB team decided to apply the solution of arranging multiple shifts to take advantage of the number of licenses available. However, in order to increase work efficiency and develop sustainably, CBB needs a more optimal solution than that temporary answer.
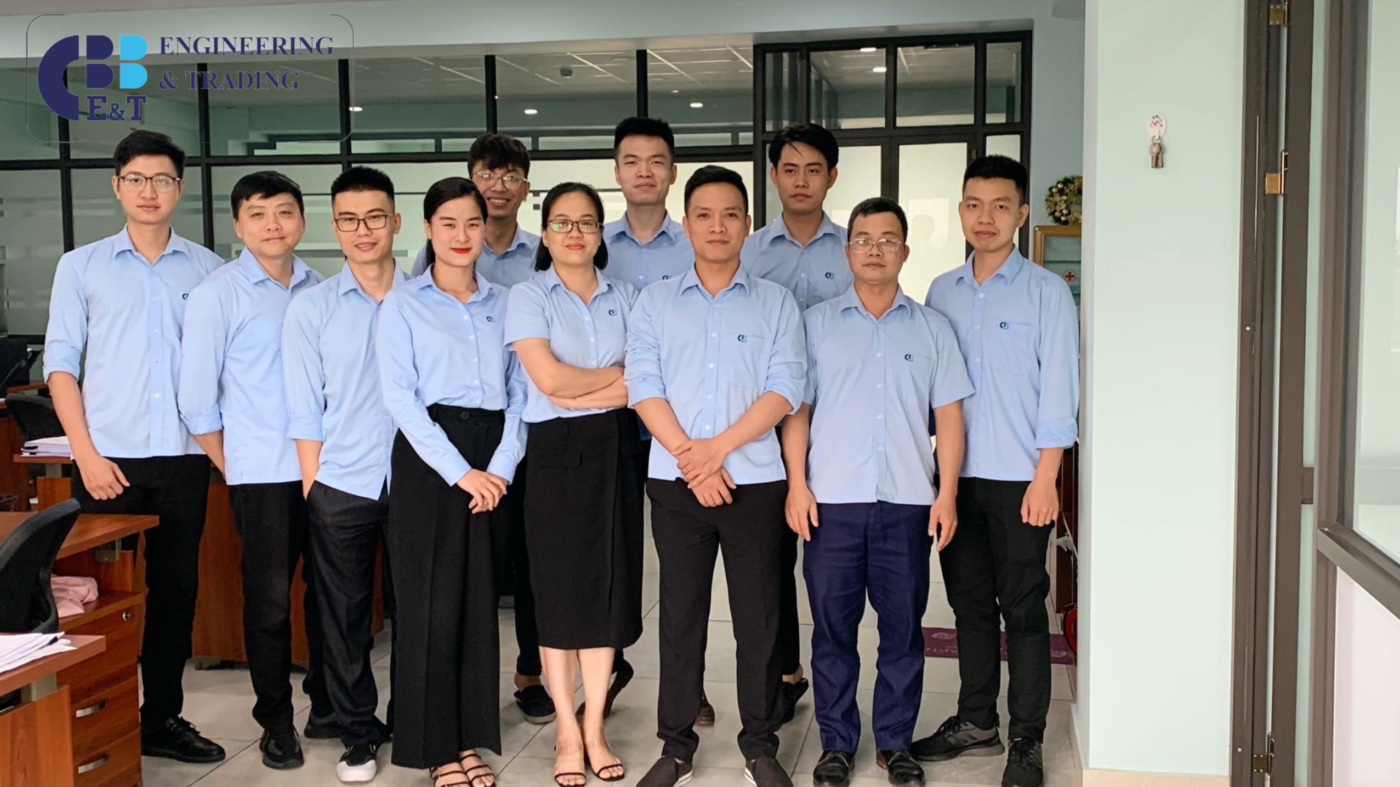
Capturing the similarity of standards applied in projects, CBB’s team of qualified and experienced Tekla API engineers researched and built a set of tools to support automated modeling. and make drawings. By inputting parameters from the input drawings along with the standard drawings provided by the customer, this toolkit can produce an automatic model with 90% completion compared to the requirements.
Some other special requirements on checking, controlling and limiting errors during modeling and drawing are also fulfilled by CBB engineers using Tekla API solution application.
Problem | Solution | Before applying the solution | After applying the solution | |
1. Work Flow of the drawing | Use the model representation function to know the status of the drawing based on changing the colors of the Assembly and Part parts in the model. | Must be exchanged manually for drawing status. Vulnerable to conflicts when working in multi-user mode. | Check the status of the drawing with just one action. No conflicts between users | |
2. Customers request to check the bolt length according to their own calculation standards, and attach the inspection report on this content. | Use TS Open API to create Custom Properties to calculate the length residual from which to check the bolt length and output the inspection report automatically. | Manually test each location and then record the results in the inspection report. It takes a lot of time (~24 hours) because the model has a lot of bolts. | Automatically check, calculate to report the results and export the test report (excel) within a few minutes depending on the number of objects in the model. | |
3. After modifying the model and marking, there are some missing part/assembly positions resulting in discontinuous part/assembly positions. | Use the TS Open API to create a tool to check the information of part/assembly. | Check by publishing a report. Each time the revised model has to conduct a re-inspection, the operation of exporting reports and manually checking using excel takes a long time because it has to be repeated several times throughout the entire process of implementing the model as well as before sending it to the customer. | Check with just one operation within 2~3 minutes depending on the number of objects in the model.It can be done every time the model changes without taking much time and effort. | |
4. Customer request (part/assembly prefix, name, UDA) must be filled in according to customer’s rules. | Use the TS Open API to create a tool to check the information of part/assembly. | Check by publishing a report.Each time the revised model has to conduct a re-inspection, the operation of exporting reports and manually checking using excel takes a long time because it has to be repeated several times throughout the entire process of implementing the model as well as before sending it to the customer. | Check with just one operation within 2~3 minutes depending on the number of objects in the model.It can be done every time the model changes without taking much time and effort. |
With continuous development efforts, along with constantly learning and creating from the available Tekla tools, CBB Company has become a long-term partner of a number of large companies in Japan specializing in activities in the field of design, development, manufacturing, installation and maintenance, automatic parking system repair, transport machinery equipment, waste and chemical treatment.
The project “Automatic parking system”.
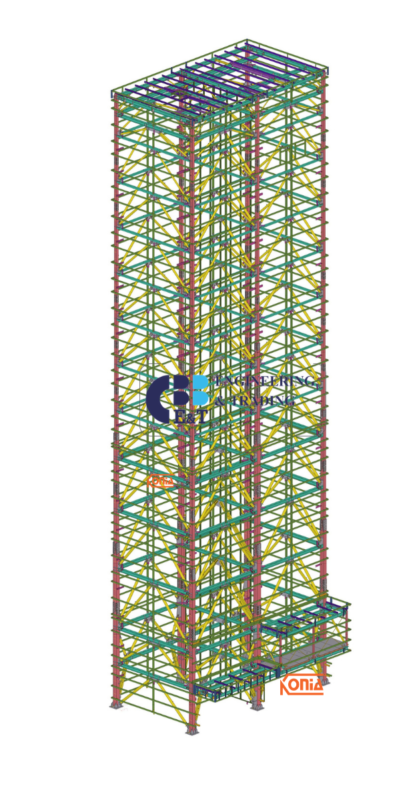
The project has a structural volume of more than 300 tons including 4 towers, two sub-towers nearly 78.5m high are divided into 24 floors and have a capacity of about 72 cars per tower, 2 main towers 115m high with a large floor beam system, divided into 34 floors and have a capacity of about 100 cars per tower.
The customer requires 20 days from signing the contract to completing the entire drawing for manufacturing. By assigning tasks, scheduling time, and effectively using the extensive toolkit and combined with the teamwork features of Trimble Connect, CBB has shortened the completion time to just 15 days
Mr. Nguyen Huy Quyen commented: “With a team of enthusiastic engineers and the investment in equipping official Tekla software, CBB has been affirming its strengths with domestic and foreign customers and partners.Over a period of time, use and develop an expanded toolkit for Tekla Structure, we have increased work efficiency by 50% in modeling and 30% in making drawings. This brings trust and appreciation from customers with whom CBB is cooperating. Thereby, we also accumulate more experience in project management and implementation in terms of progress, human resources and quality of works and projects”.